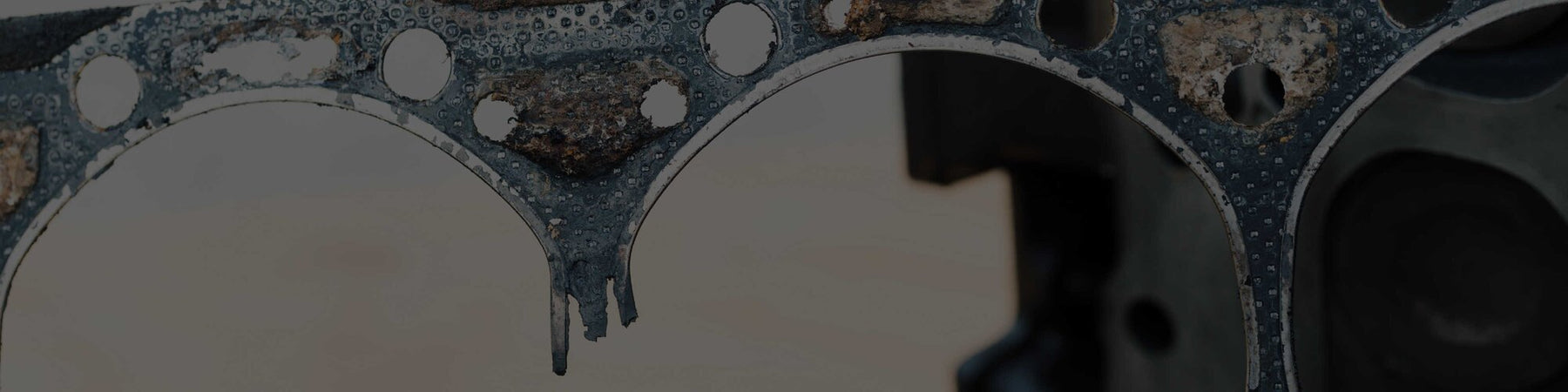
The Types of Gaskets in Heavy Equipment: Selecting The Right One For Your Machine
The Types of Gaskets in Heavy Equipment: Selecting The Right One For Your Machine
Reading time: 6 min
Introduction to Gaskets
While small in size, gaskets play an outsized role in many heavy equipment systems. Gaskets are sealing components, often ring-shaped, which are placed between two or more mating surfaces to prevent leaks and the ingress of contaminants. But unlike other types of seals, such as o-rings, gaskets come in a variety of shapes and sizes and serve a wide range of functions.
In heavy equipment, gaskets are crucial in preventing fluid leaks in the hydraulic system and engine, preventing hydraulic fluid, coolant, oil, fuel, DEF and other fluids from leaking. Additionally, gaskets protect sensitive components from contaminants such as dust, dirt and debris, which can compromise the equipment's functionality.
In this article, we’ll explore the types and functions of heavy equipment gaskets. Understanding how these components work and their roles in your equipment are key to keeping your fleet operating smoothly.
Types of Gaskets Found in Construction Machinery
Heavy equipment relies on a diverse array of gaskets. Each gasket type is designed to fulfill a specific function, crafted from materials best suited to its operational environment, and shaped to fit the unique demands of the system it seals. Here are the most common types of gaskets found in construction machinery:
1. Temperature Gaskets
Temperature gaskets are designed to withstand extreme heat or cold within machinery, often found in engine blocks, exhaust systems and around heating elements. Materials like silicone, which remains stable across a wide temperature range, or metal gaskets coated with heat-resistant compounds, are commonly used.
The shape and size of these gaskets are tailored to provide an effective seal in spaces where temperature fluctuations are significant, ensuring the machinery operates efficiently without risk of overheating or freezing.
2. Pump Gaskets
Pump gaskets are essential for maintaining the integrity of fluid movement systems within heavy equipment. These gaskets can be made from rubber, PTFE or other flexible, durable materials that can withstand the chemical composition and pressure of the fluids being pumped. Typically found between pump housing and mating surfaces, their design is crucial for preventing leaks that could lead to pump failure and operational inefficiencies.
The choice of material and the precise engineering of these gaskets ensure that they can endure the mechanical stress and corrosive environments they're exposed to.
3. Muffler Gaskets
Muffler gaskets seal the exhaust system, preventing harmful gasses from leaking into areas where operators or machinery function.
Made from high-temperature resistant materials like graphite or composite fiber, they are designed to endure the corrosive environment of exhaust fumes and the extreme heat of the exhaust system. Their effectiveness is vital not only for operational efficiency but also for the safety of the work environment, making their durability and design critical considerations.
4. Head Cover Gaskets
Located on the engine's cylinder head, head cover gaskets seal the top of the engine block, preventing oil leaks and barring contaminants from entering the engine. These gaskets are often made from rubber or cork, materials chosen for their compressibility and ability to form a tight seal despite the engine's vibrations and heat.
Their design is tailored to match the complex contours of the engine head and cover, ensuring a precise fit that maintains the engine's performance and longevity.
5. Engine Gaskets
Engine gaskets include a wide range of types involved in sealing various parts of the engine, including the head gasket, oil pan gasket and intake manifold gasket. These are typically made from multi-layer steel (MLS), graphite or other composites that can withstand the engine's pressure, temperature and chemical exposure.
The head gasket, for example, must resist high combustion pressures and temperatures, making the choice of material and its thermal and pressure resistance paramount. The design of engine gaskets is complex, matching the intricate shapes of engine components to ensure a perfect seal and prevent leaks that could lead to engine damage.
Design and Functionality of Gaskets in Heavy Equipment
At the core of a gasket’s functionality is its ability to maintain a seal under varying pressures, temperatures and environmental conditions. This sealing capability is heavily influenced by the gasket's design, including its shape, material composition and the way it is installed between machine parts.
Sealing Pressure and Gasket Design
The design of a gasket plays a crucial role in its ability to withstand sealing pressure.
For example, spiral wound gaskets are designed with a mix of metal and filler material, allowing them to maintain their seal under fluctuating pressure and temperature conditions. This is especially important in parts of machinery where pressure can vary significantly, such as in hydraulic systems.
Material Selection Criteria
The criteria for selecting gasket material hinge on several key factors:
- Temperature Resilience is key for gaskets placed near engines or exhaust systems, where temperatures can reach very high levels. Materials like graphite or metal alloys are chosen for their ability to withstand high temperatures.
- Chemical Resistance is necessary for gaskets exposed to oils, coolants or hydraulic fluids, requiring materials like Viton or Nitrile rubber that can resist these substances.
- Compressibility allows a gasket to adapt to the contours and imperfections of the mating surfaces, creating a more effective seal. Materials are selected based on their ability to compress without losing their sealing properties.
Gasket Types by Machine Area
In heavy equipment, different areas require specific types of gaskets due to varying conditions.
Near the engine, you will find head gaskets, exhaust manifold gaskets and oil pan gaskets, often made from materials that can withstand high temperatures and pressures — such as metal alloys or graphite.
In the hydraulic system, O-rings and bonded seals made from elastomers like nitrile are common, offering the necessary flexibility and chemical resistance to maintain the integrity of the hydraulic fluid flow under varying pressures.
Cooling systems use gaskets like water pump gaskets, made from rubber or silicone, to ensure the cooling fluid remains contained, preventing overheating.
Maintenance and Replacement
Regular gasket inspections are essential, with the frequency depending on the equipment's usage intensity and the environmental conditions it operates within. Typically, gaskets should be inspected at least annually or according to the manufacturer’s recommendations.
While cleaning a gasket is not usually recommended due to the risk of damaging its integrity, keeping the area around the gasket clean is important to prevent dirt and debris from compromising the seal.
In the short term, a failing gasket can lead to equipment downtime and decreased efficiency. Over the long term, ignoring these signs can result in severe damage to critical components, leading to costly repairs or replacements.
Replacing a typical gasket involves several basic steps:
- Disassembly: Remove the parts or components held together by the gasket.
- Removal: Carefully remove the old gasket without damaging the mating surfaces.
- Cleaning: Clean the surfaces where the gasket will be placed, ensuring they are free of old gasket material and contaminants.
- Installation: Place the new gasket, ensuring proper alignment and reassemble the components, following the manufacturer’s torque specifications.
Potential challenges during this process include difficulties in removing old gasket material, which may require special tools or chemicals in order to ensure a clean, smooth surface for the new gasket to seal effectively.
Final Thoughts
Gaskets, while seemingly minor components, play a critical role in maintaining the operability of heavy equipment. The integrity of gaskets directly influences the effectiveness and reliability of construction equipment, making gasket maintenance a crucial part of maintaining your fleet.
We recognize the crucial role of gaskets, that’s why the EquipmentShare Shop offers a comprehensive selection of OEM and aftermarket gaskets to meet the diverse needs of construction equipment. Search the collection and get fast shipping on a variety of gasket types. Still can’t find the exact one you’re looking for? Contact one of our parts experts and get personalized assistance.
Back to Parts In Depth
Are you signed up for our newsletter?
We'll send you a monthly email covering everything from specialty parts to machine overviews, packed with tons of knowledge from our industry pros and no filler.
SIGN UP →